-
Address: Suzhou City, Jiangsu Province, China, 215000
-
Tel: 0086-512-68235075
Maintenance Tips for Linear Bearing Blocks and Rails
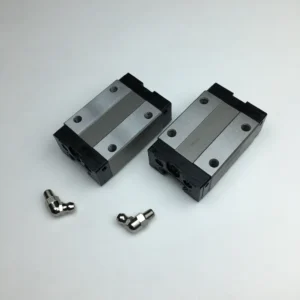
If you want to use linear bearing blocks and linear guideways for a long time, reasonable maintenance and care are the key. Linear bearing blocks and linear guideways are both components of high-precision linear motion systems, and have high maintenance requirements. The maintenance process includes key links such as cleaning, lubrication, inspection, and environmental control. A little carelessness will damage the accuracy and use of linear bearing blocks and linear guideways. This article will discuss in detail the matters that you should pay attention to during maintenance.
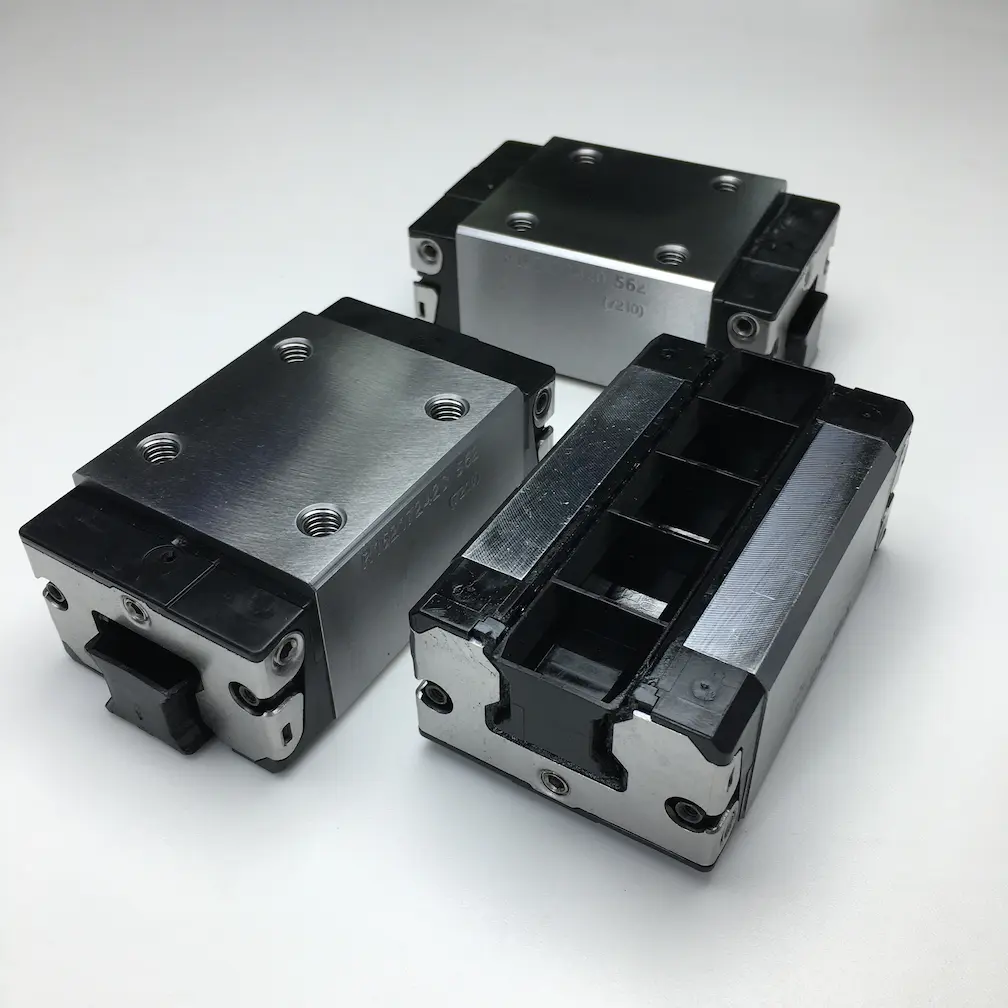
Precautions In Cleaning
- Tool selection: Use a soft brush, non-woven fabric, or compressed air to remove dust and metal chips on the surface of the guide rail. Stubborn stains can be wiped with a neutral detergent, and corrosive solvents such as alcohol should not be used.
- Cleaning frequency: After using linear bearing blocks and linear guideways for a certain time, there will inevitably be floating dust and material chips on the linear guideways. It is best to clean them regularly, such as twice a week or every certain number of kilometers. For the woodworking industry or foam processing industry, it is best to clean them daily. A clean environment can extend the life cycle of the product.
Lubrication Management
- Most linear bearing blocks are pre-coated with lubricating grease by the manufacturer when they are shipped. Generally, no additional lubricating grease is required for the first operation to meet the needs of the trial operation. After installation and trial operation, lubrication is required again. It is strongly recommended to use the same lubricating grease as the factory to avoid mixing and possible performance degradation.
- Cleaning after lubrication: Before lubrication, make sure that there are no impurities on the surface of the guide rail. After lubrication, wipe off excess grease to prevent contamination.
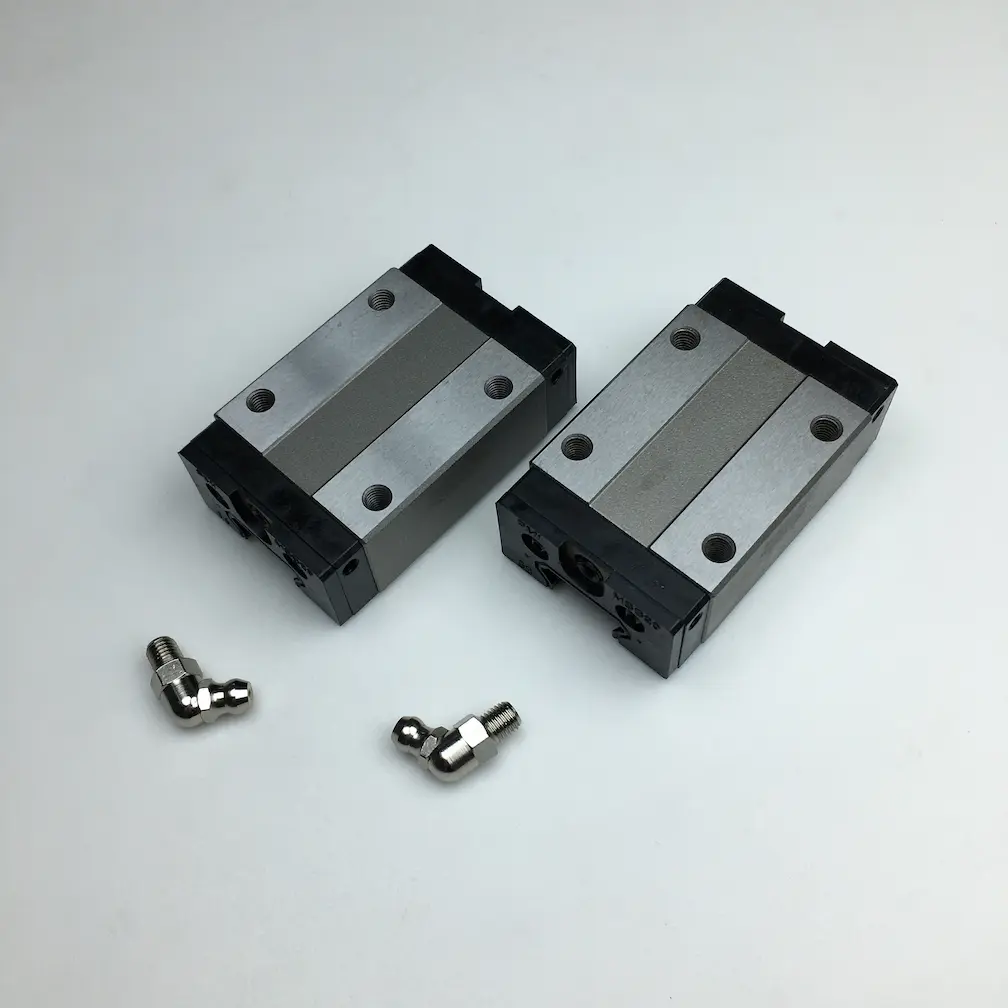
Anti-rust Areatment:
Anti-rust oil is applied around the guide rail. If cleaning is required, please disassemble the linear bearing block first to prevent foreign matter from remaining. When lubricating, re-apply lubricant to prevent corrosion. When operating the slide, be sure to wear gloves to prevent sweat from dripping on the linear bearing block or linear guideways and causing corrosion. Even if the machine is not turned on, for the service life of the linear guideways, anti-rust oil should be applied at least once every half a month. If it is in a humid environment, the frequency needs to be increased.
Plastic Parts Cleaning
Don’t use organic solvents (such as medical alcohol, disinfectants, strong glue removers, paint thinners, industrial cleaners, etc.). Linear bearing block seats are composed of plastic parts (such as seals and cages). If organic solvents are used, they are likely to cause deformation or embrittlement of the linear bearing seat, thereby reducing its accuracy. It is recommended to wipe with clean water or special cleaning agents.
When cleaning, it should be noted that the balls/rollers in the linear bearing seat are easily affected by dust and metal chips. It must be noted that rude disassembly may cause the balls to fall off or the tracks to be misaligned, thereby destroying the accuracy.
Daily maintenance and care of linear bearing seats and linear guides are an indispensable part, just like motorcycles. If you do not pay attention to maintenance, the performance of even the best products will be impaired, and even its service life will be shortened.
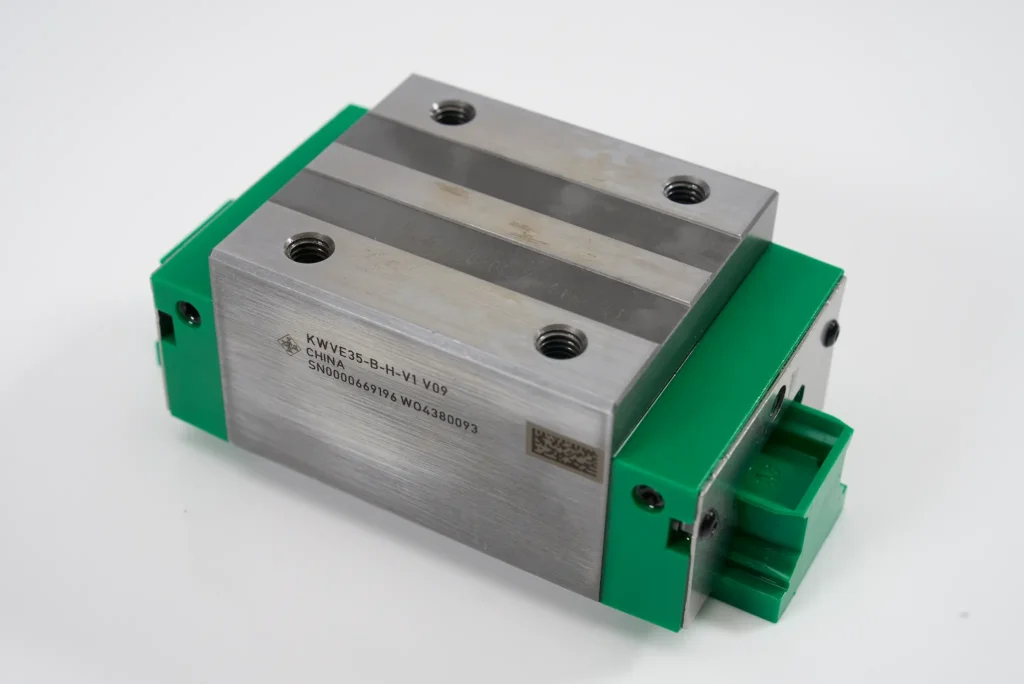
Conclusion
Therefore, maintenance is so necessary. If you still have questions about how to maintain linear bearing blocks and rails, you can refer to the official manual or video for more detailed information.