-
Address: Suzhou City, Jiangsu Province, China, 215000
-
Tel: 0086-512-68235075
How to Choose the Right Linear Rail Blocks
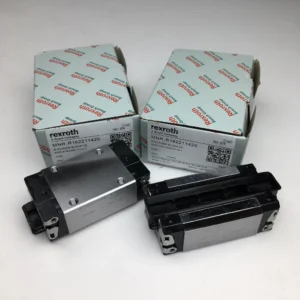
Introduction
Overview of Linear Rail Blocks and Their Applications
Linear motion guides are the fundamental core components for achieving controlled, low-friction linear movement in precision machinery. As a transmission element for linear motion, the linear rail block integrates rolling elements (balls or rollers) that circulate within the system. Its design and construction directly determine the performance characteristics of the linear motion system.
Before selecting a suitable rail block , it is crucial to be familiar with the product series from different brands. Different brands may adopt varying standards or nomenclature (e.g., THK’s “LM Guide” vs. HIWIN’s “Linear Guide”), so you must understand the differences between product series to make informed choices. When selecting products, you must consider them comprehensively based on actual requirements. If you choose the wrong model or series, it may lead to a series of problems such as: poor performance (e.g., insufficient accuracy, excessive vibration), increased maintenance, or design redundancy and high cost.
Key Design Features of the Different Linear Rail Block Series
1. Rolling Element Type (Ball vs. Roller)
Ball-type Rolling Elements:
Generally provide smoother motion, lower friction, and higher speed capability. The ball forms point contact with the raceway (or conformal contact in arc groove design). Suitable for applications requiring high speed, smooth operation, and medium load capacity. For example, HIWIN’s HG, EG, CG, QH, QE, QW series use ball-type rolling elements; THK’s HSR, SHS, SSR, SRS, SCR, EPF series also adopt ball-type rolling elements.
Roller-type Rolling Elements:
Form a larger contact area (line contact) with the raceway, resulting in significantly higher load capacity and rigidity compared to ball-type elements of the same size. Roller-type elements are the preferred choice for heavy-duty applications, machine tools requiring high rigidity, and scenarios with high impact loads. For instance, HIWIN’s RG and QR series use roller-type rolling elements; THK’s SRG, SRN, SRW, and HRX series utilize roller-type rolling elements; PMI’s MSR series employs full rollers.
The selection between balls and rollers establishes the foundation for performance trade-offs: balancing load capacity/rigidity against speed/smoothness, noise, and maintenance intervals. Rollers enhance load capacity and rigidity by expanding the contact area through line contact.
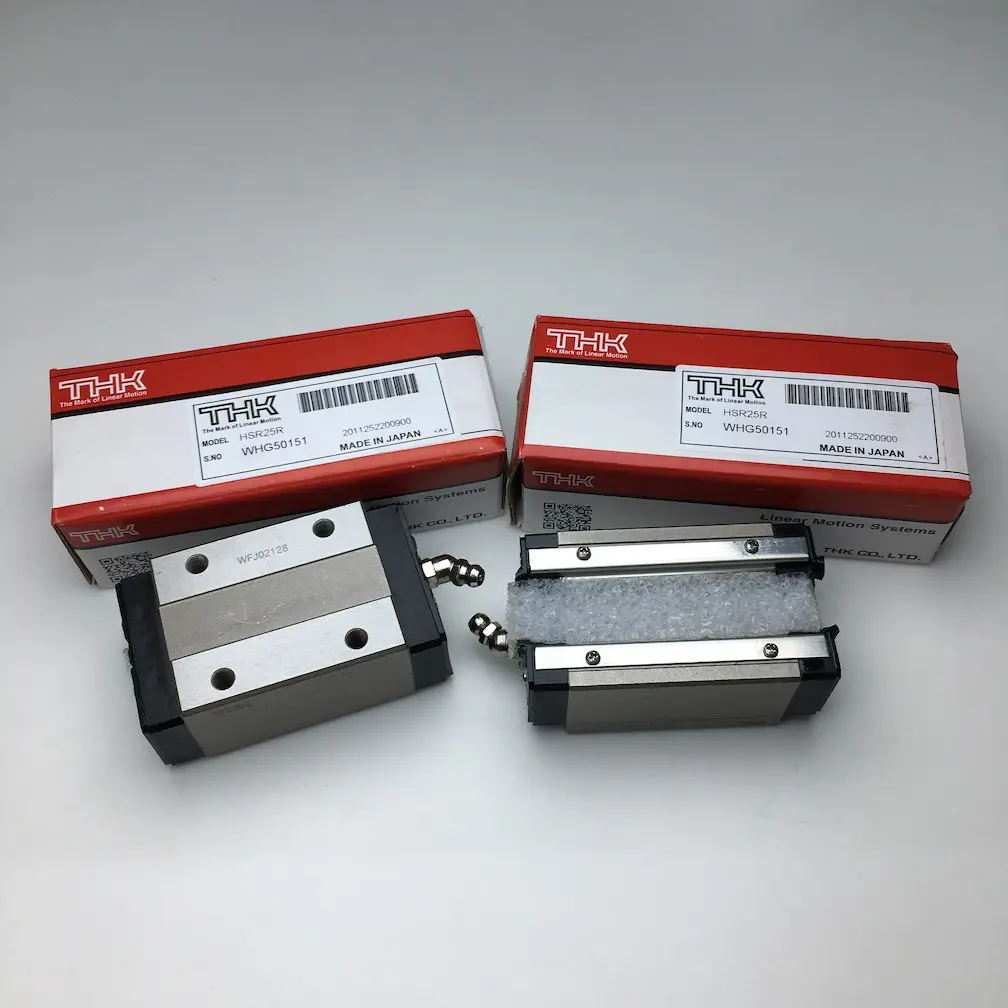
2. Cage Technology (With Cage vs. Full Roller Complement)
Full Complement Type:
Maximizes the number of rolling elements within a given volume, resulting in higher static and dynamic load capacity. However, friction between balls or rollers may result in greater noise, wear, and heat, which may limit speed. For example, THK HSR is a full-ball type; INA KUVE and KUSE are full-ball types.
Cage Type (e.g., ball separator, roller separator, SynchMotion™ technology):
A separator (cage or chain) is integrated between rolling elements to prevent mutual friction. This enables smoother operation, lower noise, higher permissible speeds, extended lubrication intervals, and more uniform motion. For example:
THK SHS, SSR, SRG series: Use ball/roller separators.
HIWIN QH, QE, QW, QR series: Employ SynchMotion™ technology (a proprietary cage system).
ABBA BC series: Ball-type with separator design.
Full Complement Design enhances static load capacity by maximizing rolling elements. However, direct contact friction between elements generates noise and heat, limiting operating speeds. Cage technology reduces noise, enables higher speeds, and improves lubricant retention by eliminating direct contact, though some load rating may be sacrificed compared to a full-complement design of the same frame size.
3. Load Capacity and Rigidity
Four-Way Equal Load Distribution:
Many modern designs (e.g., HIWIN HG, EG, WE, RG; THK HSR; PMI MSA) employ specific rolling element geometries (typically 45° contact angle) that enable the linear rail block to carry equal or nearly equal loads in radial, reverse radial, and lateral directions. This provides versatility in mounting orientation and load application.
Moment Load Capacity:
The ability to resist moments (Mx, My, Mz) is critical, especially in single-track applications or when offset loads are present. Wide track designs (e.g., HIWIN WE, QW; THK SHW; PMI MSG) or specific bearing arrangements (e.g., O-type configuration of HIWIN CG) enhance moment load capacity.
4. Accuracy and Preload
Accuracy Grade:
Manufacturers offer a variety of accuracy grades (e.g., HIWIN Normal Grade (C/N), High Grade (H), Precision Grade (P), Super Precision Grade (SP), Ultra Precision Grade (UP); THK; PMI; INA; Rexroth). Higher accuracy grades mean tighter dimensional tolerances and smoother motion, which is critical for precision machinery.
Preload:
Applying preload can eliminate internal clearances, thereby improving rigidity and accuracy, but it also increases friction. Manufacturers offer different preload levels (e.g., light preload, medium preload, heavy preload) to balance these factors.
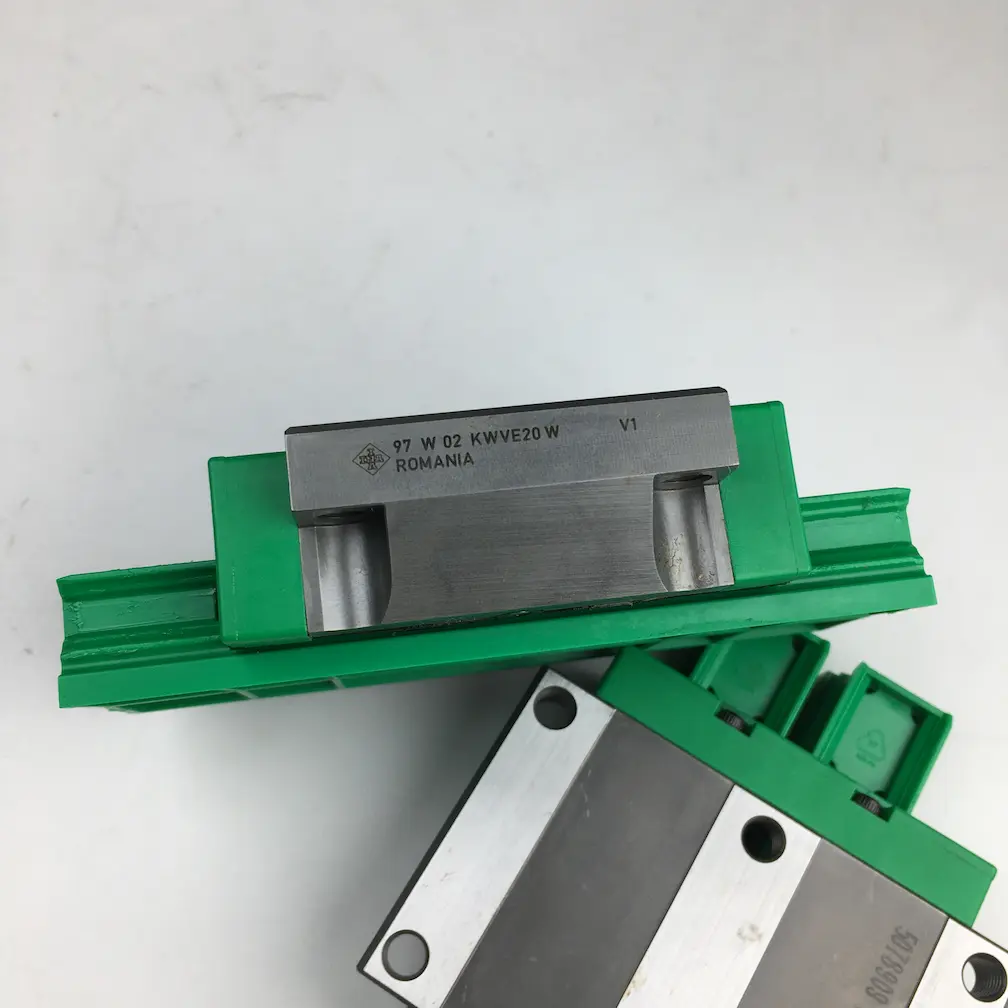
5. Special Features
Miniature Linear Rail Block Series:
For compact applications such as medical equipment, semiconductor handling, and small automation equipment. For example, HIWIN MG Series, THK SRS Series, PMI MSC/MSD Series; ABBA BM Series.
Integrated Lubrication Systems:
Integrated lubrication units (e.g., HIWIN E2; ABBA BR; THK QZ Lubricator) extend maintenance intervals and improve reliability.
Contamination Resistance & Sealing:
Various sealing options (face seal, bottom seal, scraper, protective cover strip) prevent the ingress of contaminants, which is critical for harsh environments or to maintain cleanliness.
Materials:
Standard material is typically carbon steel, but stainless steel options are also available (e.g., HIWIN MG Series; THK HSR, SSR stainless steel option) for corrosion resistance or specific industry requirements (e.g., food, medical).
Noise Reduction Technologies:
Features such as HIWIN’s SynchMotion™ Technology or THK’s Ball/Roller Cage Technology are designed to reduce operating noise.

Special Design Features
Misalignment Compensation:
The misalignment compensation feature (e.g., HIWIN HG, EG; THK HSR) is critical in practical applications, as perfectly machined and aligned mounting surfaces are both expensive and difficult to achieve. Tolerances always exist in manufacturing and assembly processes. If a linear guide system is extremely sensitive to minute misalignments of the mounting surfaces, extremely high-precision machining and careful installation are required. The misalignment compensation feature, often achieved through specific rolling element geometries (such as HIWIN’s 45-degree contact angle arc groove), allows the linear rail block to slightly adjust or “absorb” these errors. This reduces stress concentrations, ensures even load distribution on the rolling elements, and results in smoother motion and longer service life even when mounting conditions are less than perfect.
Interchangeable Linear Rail Block Series:
The popularity of interchangeable Linear Rail Blocks series (e.g., HIWIN HG, EG, RG, QH, QE, QW, QR; ABBA BR, BC; PMI; Rexroth) reflects the market’s demand for flexibility in design, procurement, and maintenance. Historically, high-precision guides often required that the rail block and rail be factory-matched pairs. If one component failed, the entire assembly might have to be replaced. Interchangeable systems mean that rail blocks and rails of the same series and size (and often accuracy class) can be sourced and replaced independently. This simplifies inventory management for manufacturers and end users, reduces downtime during repairs, and provides greater flexibility during machine design. When mixing components from different batches, You can still maintain a certain level of accuracy (e.g., P-level accuracy for HIWIN EG interchangeable type). What an Engineering Achievement!
Conclusion
The selection of linear rail blocks requires comprehensive considerations, because once the wrong choice is made, minor problems will continue to occur. For example, the wrong preload grade selection will cause excessive wear of the rail block . Anyway, this will cause a decrease in accuracy and improper travel . There are many such problems. These problems will undoubtedly reduce the efficiency of machine processing. Therefore, it is best to understand the professional knowledge or contact a dedicated salesperson before purchasing.